I am just starting to build the front cowl master model. The process stated with the construction of the Spinner master model. The spinner surface was designed to allow the cowling loft lines to blend in the side profile and the top or max half breadth profile to the rest of the fuselage. consequently its oversize from the typical spinner one usually sees on an ultralight or conventional airplane. I took the surface loft directly from my 3D model and intersected it with planes spaces 3/4" apart. I then plotted all of them out together and made a plot of the combined stack up. I also plotted a 1" diameter hole in the center that was common to each section. This was to allow all of the sections to be aligned on a 1" diameter tube. I cut all of the sections out from a sheet of MDH board. I stack glued them together and then mounted the stack up on my lathe.
 |
MDH sections bonded and mounted on a face plate |
MDH board is a good material to use for this master model, it is basically pressed sawdust and because of this it has no grain direction. It will smooth and work evenly in all directions. The stack up was mounted to an aluminum face plate to allow me to chuck it onto the lathe. I stated turning the stack up. The actual loft contour line is at the bottom of each circle.
 |
spinner master being turned down |
I set up a tool fence on my metal lathe similar to that used on a wood lathe. I worked the stack up using conventional wood lathe chisels. This was a relatively quick job. It wasn't long before the final shape started to emerge.
 |
Master after sanding and before a coat of Bondo. |
At this point the surface had to be coated with a light coat of Automotive body filler or "bondo" to fill in all of the surface pores and to allow for the final smooth finish.
 |
Master with a surface coat of Bondo |
After the Bondo was applied, it was sanded down smooth. Subsequent coats were added and each time a finer and finer grit of sand paper was used. Eventually the surface was painted with sand able primer and then further filled with spot putty. The final surface was sanded with 400 grit sand paper and a top coat of urethane automotive paint was applied. From this "plug" or Master model I then made a female mold. At the same time I built the Spinner mold I also made the Horizontal/Elevator tip cap mold. It was more efficient to shoot the Gel coat when I had a second mold to produce.
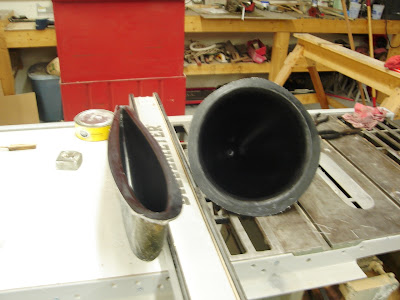 |
Spinner and Horizontal Tip cap molds. |
Both of these molds will be wet sanded with 600 grit paper and then "seasoned" with up to 12 coats of carnuba mold release wax.
As I mentioned earlier I made the original Spinner plug with 1" diameter holes to use for alignment. The secondary purpose of this was to allow the original plug to be temporally mounted to the engine prop flange So I can start the shaping process of the cowl master model. I will again use my floral foam method to shape the cowl surface. There will be a sub frame built to support the foam blocks while they are shaped and to eventually allow the foam master to be slipped off the fuselage so a plaster splash can be taken. Here is a picture of the spinner in place before the foam is added.
 |
Spinner Master attached to prop flange |
No comments:
Post a Comment